Thermal Modification Kiln
-
-
Before Thermal Modification
-
After Thermal Modification
-
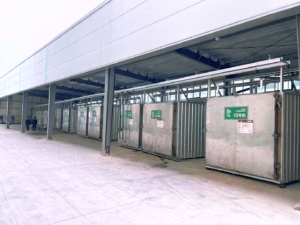
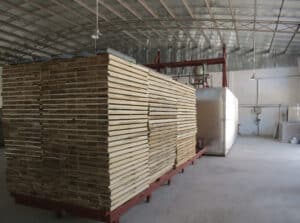
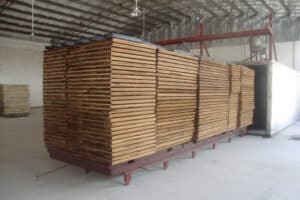
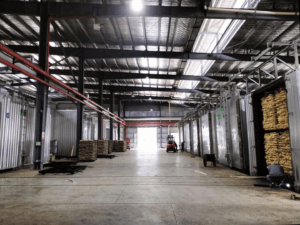
Thermal Modification Kiln
In the thermal modification kiln, the wood undergoes a processing stage at elevated temperatures spanning from 160°C to 250°C (320°F to 482°F) in an oxygen-free environment. This heat-treated modification mechanism significantly enhances the wood’s inherent characteristics, improving dimensional stability, boosting resistance to decay and weathering. The resulting eco-friendly wood is not only highly durable but also has an appealing and uniform color.
Hardwood, Softwood and Bamboo
160 - 250 °C (320 - 482 ℉) Heat Treatment
Thermal Break and Air Circulation Tech
Durable and Safe
Thermal Modification Kiln Specification
Specification | Details |
Model | HMY/HMD |
Capacity | 20 – 40m³ (Customizable for other sizes) |
Maximum Temperature inside the Kiln | 250 ℃ (482℉) |
Applicable Lumber Types | Softwood, Hardwood and Bamboo |
Loading Method | Rail and Trolley |
Kiln Structure Material | 304 Stainless Steel Inner Wall |
Heating Medium | Electricity / Thermal Oil |
Site Requirements | Indoor / Under Shelters |
Thermal Modification Kiln Specification
Specification | Details |
Model | HMY/HMD |
Capacity | 20 – 40m³ |
Maximum Temperature Inside the Kiln | 250 ℃ (482℉) |
Applicable Lumber Types | Softwood, Hardwood, and Bamboo |
Loading Method | Rail and Trolley |
Kiln Structure Material | 304 Stainless Steel Interior |
Heating Medium | Thermal Oil/ Electricity |
Site Requirements | Indoor |
Features of Thermal Modification Kiln
Air Circulation Technology
✅ External motor with the unique design of the fan shaft structure and bearing lubrication enables the fans to be positioned anywhere within the kiln as required. This allows for precise regulation of the air dynamic circulation, ensuring a uniform heat flow distribution. Consequently, the drying uniformity and efficiency of the lumber are enhanced.
Thermal Break Technology
✅ With a 150–200mm high-performance insulation layer and advanced thermal break technology, the system effectively minimizes heat loss by interrupting heat conduction paths through the kiln structure.
Construction for Enhanced Durability
✅ The interior of the kiln is made of 304 stainless steel, offering excellent corrosion resistance and a long service life.
Inert Gas Protection-Free Design
✅ Designed for high efficiency and energy savings, the system eliminates the need for inert gas protection like steam, reducing energy consumption and simplifying operation.
Safe Operation
✅ During the thermal modification process, gases flow outward only, preventing oxygen from entering and greatly reducing the risk of ignition.
Smart Control
✅ The smart control system enables precise regulation of temperature and humidity. It enables remote control and real time data management , ensuring user friendly, along with high efficiency and energy conservation.
What is Thermal Modification or Heat Treatment of Wood?
Definition: Wood carbonization (thermal modification) refers to the heat treatment of wood at high temperatures ranging from 180 to 250 °C.
Principle: High – temperature degrades hemicellulose in wood. The generated organic acids speed up the degradation of hemicellulose and cellulose’s amorphous regions, reducing hygroscopic hydroxyl groups and increasing the crystalline region, thus enhancing dimensional stability. Degradation produces organic acids and phenolic compounds that inhibit decay – causing fungi, strengthening decay resistance. With fewer hygroscopic hydroxyl groups, the wood’s outdoor moisture content variation lessens. High – temperature treatment also creates photo – aging – resistant compounds, improving weather resistance. Difference from Surface Carbonization: It is not surface carbonization for decoration only, but uniform carbonization across the whole wood cross – section.
Product and Its Advantages: The product is thermally – modified wood (carbonized wood), boasting excellent dimensional stability, decay resistance, and weather resistance.
Application: It is especially suitable for geothermal floors and outdoor use.